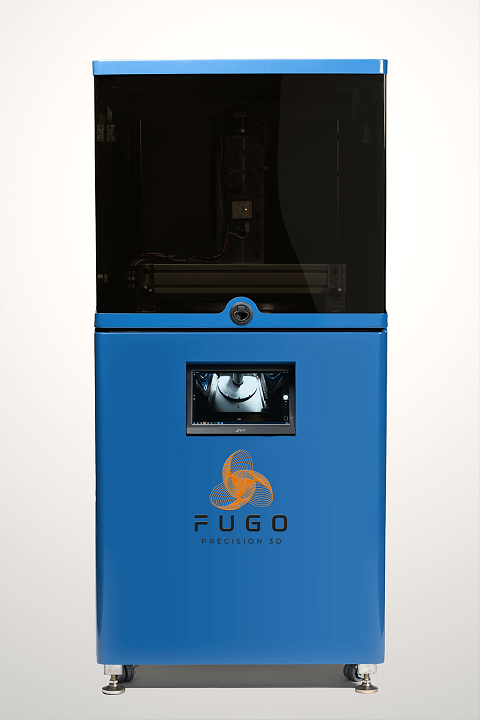
3D Printing Information Briefs, August 10, 2024: Centrifugal 3D Printer, Waveguides, & Extra – 3DPrint.com
In 3D Printing Information Briefs, an organization has launched what it says is the primary centrifugal 3D printer, AIM3D secured patents for pellet 3D printing, and micro-CT scanning is getting used for real-time print monitoring. Transferring on, Quickparts launched a brand new on-line instrument to streamline quantity manufacturing requests, and a US Air Power base put in a brand new 3D printer in its metals store. Lastly, researchers in Australia are 3D printing low-cost augmented actuality optical waveguides.
Fugo Precision 3D Launches Centrifugal 3D Printing Know-how
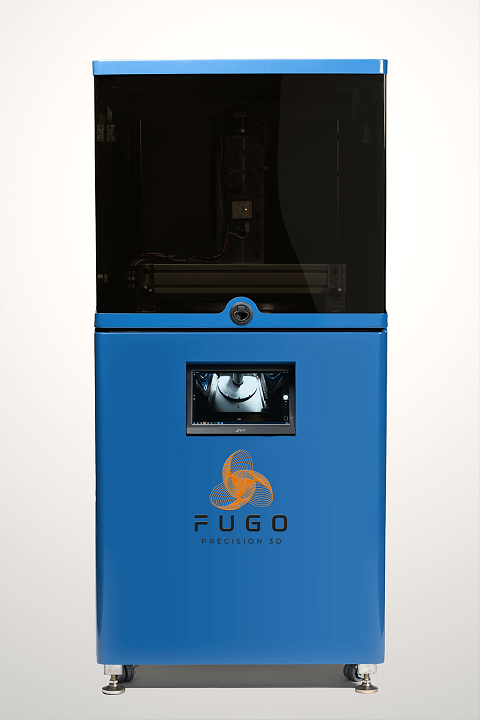
Fugo Mannequin A
At RAPID+TCT 2024 in Los Angeles, Fugo Precision 3D unveiled what it calls the world’s first centrifugal 3D printer, which is a serious milestone within the evolution of additive manufacturing. Now formally launched, the Fugo Mannequin A is alleged to supply patented “layerless” 3D printing with sub-30-micron accuracy, in addition to elevated velocity and throughput as much as ten instances sooner than conventional SLA 3D printers. The printer works with a number of functions and a variety of photopolymers, and the corporate is concentrating on high-volume producers that use 3D printing as a essential ingredient in manufacturing strains. The Fugo Mannequin A lowers prices and improves effectivity by integrating a number of post-production processes to streamline the workflow, so customers can supposedly print, wash, dry, and post-cure components with out having to make use of a number of machines. Preliminary business manufacturing machines must be delivered in Q1 of 2024, and Fugo is now taking reservations for the Mannequin A.
“For the reason that introduction of SLA and DLP expertise, the one best drawback with these printers has been the necessity for a mechanical means to unfold the infinitely skinny layers,” mentioned Sasha Shkolnik, CTO of Fugo Precision 3D. “With the Fugo Mannequin A, we’ve solved this drawback as our expertise doesn’t use any mechanical means to create layers throughout printing.”
AIM3D Secures Patents in U.S. & Europe for 3D Pellet Printing
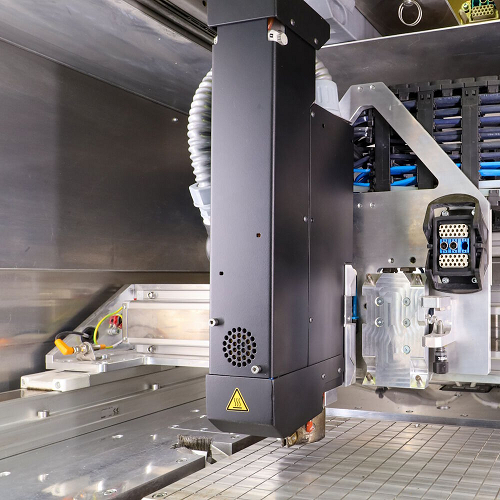
CEM extruder nozzle (nozzle sizes from 0.3 mm to 0.6 mm) for Examination 255 and Examination 510 from Purpose 3D
German 3D printing firm AIM3D, a College of Rostock spin-off, has secured patents in each the U.S. and Europe that shield its work in 3D extrusion printing. The corporate’s focus is pellet 3D printers, and the 4 patents cowl its composite extrusion modeling (CEM) expertise for high-temperature materials extrusion 3D printing, decentralized pellet extruders, and, within the U.S., its high-flow scorching ends and filament extruders. The patented CEM expertise permits for prime construct charges and uniform extrusion, and is particularly efficient at processing ULTEM 9085, which is usually utilized in aerospace functions. The corporate’s industrial Examination 255 and Examination 510 printers can deal with ceramics, polymers, and metals, and have a value benefit over conventional FDM programs, as they use customary pellets with or with out fillers. Plus, its Voxelfill technique addresses inhomogeneous strengths in 3D printing, which makes it attainable to attain diminished materials and weight, in addition to custom-made materials properties.
“The granted patents replicate our spectacular achievements in analysis and improvement. These patents safe our know-how for 3D pellet printers. On the identical time, we’re open to establishing licensing partnerships,” mentioned AIM3D’s CEO Dr.-Ing. Vincent Morrison.
Utilizing Dynamic Micro-CT for Actual-Time Monitoring of 3D Printed Elements

Determine 2. (prime) load curve displaying measured pressure over instances; (backside) instance pictures of every pattern at completely different instances through the check. Picture Credit score: TESCAN USA Inc.
Whereas 3D printing opens up many new prospects in superior manufacturing, it’s vitally necessary to work on gaining a greater understanding of a 3D printed half’s efficiency whereas in operation—particularly when it’s confronted with exterior circumstances like loading or heating. Standard mechanical testing strategies present a normal overview of the half’s mechanical properties, however the impression can solely be decided by damaging strategies on the finish. A greater manner is dynamic micro-CT scanning, which permits uninterrupted knowledge assortment and may be very helpful for non-destructive evaluation of the intricate geometries present in 3D printed components. Just lately, the TESCAN UniTOM XL micro-CT was used for real-time monitoring and knowledge acquisition in a research of the modifications that inside constructions of 3D printed plastic components endure throughout compression loading.
Micro-CT scanning makes use of x-rays to gather 3D knowledge, and utilizing the expertise in situ permits for a three-dimensional research of processes inside a pattern half underneath altering exterior circumstances throughout mechanical testing. Information may be captured throughout your complete course of utilizing this technique, because of the excessive temporal decision that’s utilized by dynamic CT. A research was carried out of in situ 3D deformation of three plastic components, every 3D printed with a distinct, frequent infill sample—Cross 3D, Dice, and Triangle. Whereas every pattern was constantly compressed, 220 tomograms had been captured over 22 minutes utilizing the TESCAN UniTOM XL micro-CT, with a voxel dimension of 59 µm and a temporal decision of 5.8 seconds per pattern rotation. The person was capable of study all types of details about the inside constructions of the components, reminiscent of a transparent separation between particular person layers within the Cross 3D pattern because the load will increase; this might point out an absence of fusion between particular layers, which suggests the preliminary construct parameters must be transformed.
Quickparts Launches On-line Software to Streamline Quantity Manufacturing Requests

Quickparts offers prospects with a devoted group of undertaking, engineering and manufacturing group from the beginning of each undertaking
Customized manufacturing companies supplier Quickparts introduced a brand new on-line instrument, obtainable by its QuickQuote portal, that’s designed to streamline the request course of for quantity manufacturing. The user-friendly interface streamlines every thing and makes it simple for purchasers to add information, enter particulars like supplies, design specs, and most well-liked processes, and submit the request. Then, a speedy response is triggered from a devoted undertaking group, which lays the muse for discussions about buyer undertaking wants and customised quotes. The brand new instrument is aimed notably at prospects with advanced or large-scale initiatives in injection molding, additive manufacturing, and CNC machining, and is only one extra instance of Quickparts’ persevering with dedication to quantity manufacturing capabilities.
“We’re thrilled to unveil this new on-line instrument. This revolutionary answer simplifies the request course of for quantity manufacturing initiatives, enabling our prospects to obtain custom-made options that completely align with their particular wants,” mentioned Ziad Abou, Chief Success Officer for Quickparts. “At Quickparts, we’re devoted to delivering the aggressive edge our prospects want by offering distinctive service, unmatched high quality, and revolutionary manufacturing options.”
USAF Base Provides Stratasys 3D Printer to thirty first MXS Metals Store

U.S. Air Power Senior Airman Abram Reyes, thirty first Upkeep Squadron plane metals technician journeyman, checks upkeep components of the thirty first MXS metals store Stratasys F900 3D printer at Aviano Air Base, Italy, July 12, 2024. (U.S. Air Power photograph by Workers Sgt. Heather Ley)
The US Air Power Aviano Air Base has been utilizing 3D printing since 2019 in a number of items, together with the thirty first Upkeep Squadron (MXS). The thirty first MXS fabrication flight not too long ago added new capabilities to the steel store within the type of a Stratasys F900 3D printer and related software program. Annually, the thirty first MXS fabrication flight produces about 63 native manufactured instruments and over 350 minor plane parts, with the assistance of a 3D printer within the Wyvern Spark Lab that may solely construct components as much as 25.6 x 25.6 cm. However by utilizing the brand new in-house Stratasys expertise on the metals store as an alternative, these numbers might majorly enhance by subsequent yr, because the F900 can print components as giant as 91 x 91 cm. By 3D printing prototype molds for the components first, they will simply return and redesign if there’s a problem, with out having to begin from scratch. John Bultman, College of Dayton Analysis Institute additive manufacturing engineer, visited the store and skilled the Airmen to function, program, keep, and troubleshoot the printer.
“It opens a brand new and big selection of prospects sooner or later. Though it’s new right here, different bases have been utilizing this expertise for a number of years now and we’re very excited to have this functionality right here,” mentioned Senior Airman Abram Reyes, thirty first MXS plane metals technician journeyman.
Researchers 3D Printing Low-Value Augmented Actuality Waveguides

The tailored printing platform and the fabrication course of. Schematics illustrate the modified 3D printing platform. To reinforce mild distribution uniformity, a diffuser and an absorber had been positioned in entrance of the sunshine supply. Moreover, one other diffuser was positioned on prime of the LCD display. The highest and backside parts of the waveguide had been printed individually on glass printing beds and later built-in with the dielectric reflectors utilizing UV resin.
Utilizing a near-eye machine, it’s attainable to create an interactive expertise—augmented actuality—by projecting digital data onto real-world objects. The AR subject is widespread for enhancing leisure, and studying and manufacturing processes, but it surely’s not simple or low cost to mass produce the core light-transmitting parts in AR gadgets known as waveguides. To resolve this drawback, a group of researchers from the College of Melbourne designed a novel, low-cost method for manufacturing optical waveguides by utilizing a modified LCD 3d printer. As they clarify of their paper, the researchers 3D printed parts of a geometrical AR waveguide, utilizing UV resin to bond three dielectric reflectors and different 3D printed components. The group was capable of enhance floor roughness with out counting on dicing, molding, and post-polishing, which helps keep picture high quality of the waveguide whereas additionally decreasing prices. They plan subsequent to discover superior supplies and printing strategies to boost the efficiency and sturdiness of AR waveguides.
“The intricate nature of conventional AR fabrication strategies and their excessive precision necessities for optical traits have turn out to be vital limitations to overcoming the price of mass manufacturing. The success of our prototype suggests potential for widespread utility and commercialization,” defined creator Ranjith Unnithan.
Subscribe to Our E-mail E-newsletter
Keep up-to-date on all the newest information from the 3D printing business and obtain data and presents from third social gathering distributors.